 |
耐硫酸性試験および抗菌性試
験に関する報告書 |
2022年2月 愛媛大学大学院理工学研究科 氏家 勲 |
 |
1.実験概要 |
|
1.1
概 説
本開発研究では,日本下水道事業団の「下水道コンクリート構造物の防食
抑制技術及び防食技術マニュアル」の塗布型ライニング工法の品質規格に準じた耐硫酸性試験および活性汚泥を用いた抗菌性試験
を実施した。
1.2 防食被覆材の配合および被覆パターン
防食塗材の配合を表1.1?aおよび表1.1?bに示す。実験に用いた供試体には防食塗材を3層あるいは4層に分けて被覆し
てある。表1.2?aおよび表1.2?bは供試体の被覆パターンを示す。表1.3は銅スラグ(住友金属鉱山)および坑廃汚泥
(岩見鉱山廃汚泥)の成分を示す。
表1.1?a
抗菌防食塗材配合表(スナミヤ)
表1.1?b
抗
菌防食塗材配合表(コスモケミカルズ)

表1.2?a
塗
材被覆組み合わせ(スナミヤ)

表1.3
銅
スラグ(住友金属鉱山)および坑廃汚泥(岩見鉱山廃汚泥)の成分
銅スラグ
坑廃汚
泥

なお、全ての供試体は耐硫酸性試験に供し、抗菌性試験にはNo.2、No.3、No.5、No.6、No.8、No.10を供し
た。
1.3 供試体概要
供試体の寸法は150×70×20mmである。耐硫酸性試験においては硫酸の浸漬面以外を耐硫酸性エポキシ樹脂とパラフィンで図
1.1に示すように、供試体端部の10mmを被覆した。これは、供試体の角は防食塗材が均一に塗装できていない可能性があり、ピ
ンホールなどの不具合は生じやすく、そこから硫酸が侵入して、試験が適切に実施できなることを防ぐためである。なお。抗菌性試験
のための供試体にはこの処理は行っていない。
図?1 供試体の処理の概要

2
1.4 耐硫酸性の検討
耐硫酸性の検討は全ての供試体で実施した。このとき,硫酸に対する耐硫酸性および遮断性の判断方法は,下水道コンクリート構造物
の腐食抑制技術及びマニュアルに規定されている塗布型ライニング工法の品質規格(表1.4)を基準とした。表1.4は塗布型ライ
ニング工法の品質規格を示す。本研究開発では表1.4のC種およびD種の品質規格を満足することを目標としているため,10%の
硫酸水溶液に浸漬させた。なお,遮断性については120日間浸漬した後に硫黄侵入深さを電子線マイクロアナライザー(EPMA)
で分析することが原則となっているが,本研究開発では耐硫酸性を満足し,120日間の浸漬後に供試体を切断し,フェノールフタレ
イン法より呈色させて,供試体内部のモルタルが中性化していないことを確認してから,EPMAによる分析を行うこととした。
表1.4 塗布型ライニング工法の品質規格

1.5 抗菌性の検討
抗菌性の検討は,供試体No.2、No.3、No.5、No.6、No.8、No.10で実施した。松山市中央下水道浄化セン
ターの汚泥濃縮ピット内から活性汚泥を採取した。図1.2は汚泥活濃縮ピット内を示す。活性汚泥には,多くの細菌が含まれている
が,硫酸発生の起因となる硫黄塩還元菌と硫黄酸化菌も存在する。各供試体の抗菌性を検討するために供試体1つずつ違う容器で行っ
た。また,比較のために供試体の入っていない場合も試験を行った。試験は7日間で,図1.3のように曝気した状態で行った。これ
は,好気性細菌である硫黄酸化細菌を活性化させるためである。また、曝気による実験結果のバラツキも考えられたので、曝気を行わ
ない場合も実施した。試験終了後,上澄みを採取し,愛媛県環境衛生研究所にて標準寒天培養地法で細菌数を検査した。標準寒天培地
法とは,種類に関わらず,生きている菌を対象に,どれくらい生息しているかを検査する方法である.

図
1.2
濃
縮ピット内

図
1.3
曝
気中の活性汚泥
|
 |
2.実験結果 |
|
2.1硫酸性浸漬試験
以下に各供試体の硫酸浸漬試験における耐硫酸性について示す。
図2.1は供試体No.1の硫酸浸漬試験状況を示す。浸漬後60日後の観察において、矢印の位置に塗材のひび割れが確認され た。
浸漬前 60日後

図2.1
硫酸浸漬試験における経時変化(No.1)
図2.2は供試体No.3の硫酸浸漬試験状況を示す。浸漬後60日後の観察において、モルタルに石膏が生成し、大きな亀裂と剥離が確
認された。
浸漬前 60日後

図2.2
硫酸浸漬試験における経時変化(No.3)
図2.3は供試体No.5の硫酸浸漬試験状況を示す。浸漬後60日後の観察において、モルタルに石膏が生成
し、大きな亀裂と剥離が確認された。
浸漬前 60日後

図2.3 硫酸浸漬試験における経時変化(No.5)
図2.4は 供試体No.7の 硫酸浸漬試験状況を示す。浸漬後60日 後の観察において、矢印の位置に塗材のひび割れが確認された。
浸漬前 60日後

図2.4 硫酸浸漬試験における経時変化(No.7)
図2.5は 供試体No.9の 硫酸浸漬試験状況を示す。浸漬後60日
後の観察において、矢印の位置に塗材のひび割れが確認された。
浸漬前 60日後

図2.5 硫酸浸漬試験における経時変化(No.5)
以上のように、表1.1?bに 示した配合で作製した塗材においては、10%の
硫酸水溶液に60日間の浸漬により、被覆に膨れとひび割れが観察されたことから、下水道コンクリート構造物の腐食抑制技術及びマニュアルに規定されている塗布型ライニング
工法の品質規格のD種を満足しなかった。
図2.6は 供試体No.2の 硫酸浸漬試験状況を示す。浸漬後60日
後の観察において、塗材表面がやや荒々しくなっているが、膨れ、ひび割れ、軟化、溶出は観察されなかった。そこで、硫酸浸漬試験を120日
まで継続した。硫酸浸漬試験120日
での表面観察において、膨れおよびひび割れが観察されたため、硫黄浸透深さを評価項目とする遮断性については無いといえる。
浸漬前 60日後
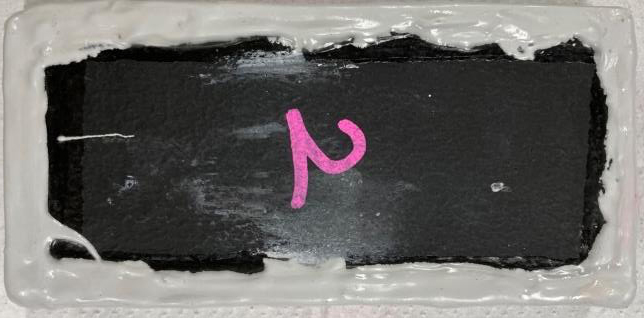
120日後
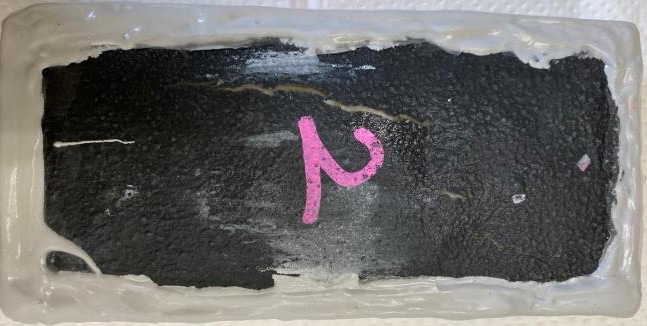
図2.6 硫酸浸漬試験における経時変化(No.2)
図2.7は供試体No.4の硫酸浸漬試験状況を示す。浸漬後60日後の観察において、膨れおよびひび割れが観察され た。
浸漬前 60日後

図2.7
硫酸浸漬試験における経時変化(No.4)
図2.8
は供試体No.6の硫酸浸漬試験状況を示す。浸漬後60日後の観察において、塗材表面の色調が変化し、小さなひび割れが観察された。ただし、ひび割れが表層のみと考えられ
たので、硫酸浸漬試験を120日まで継続した。硫酸浸漬試験120日での表面観察において、膨れおよびひび割れが観察されたため、硫黄浸透深
さを評価項目とする遮断性については無いといえる。
浸漬前 60日後

120日後 120日後(膨れ)

図2.8
硫酸浸漬試験における経時変化(No.6)
2.9は供試体No.8の硫酸浸漬試験状況を示す。浸漬後60日後の観察において、膨れ、ひび割れ、軟化、溶出は観察されなかった。そこで、
硫酸浸漬試験を120日まで継続した。硫酸浸漬試験120日での表面観察において、ひび割れは観察されなかったが、膨れが観察されたため、硫
黄浸透深さを評価項目とする遮断性については無いといえる。
浸漬前 60日後

120日後 120日後(膨れ)

図2.9
硫酸浸漬試験における経時変化(No.8)
図2.10
は供試体No.10の硫酸浸漬試験状況を示す。浸漬後60日後の観察において、塗材表面の一部に割れが観察された。
浸漬前 60日後

図2.10
硫酸浸漬試験における経時変化(No.10)
2.11は供試体No.22の硫酸浸漬試験状況を示す。浸漬後60日後の観察において、膨れ、ひび割れ、軟化、溶出は観察されなかった。そこ
で、硫酸浸漬試験を120日まで継続した。硫酸浸漬試験120日での表面観察において、膨れが観察されたため、硫黄浸透深さを評価項目とする
遮断性については無いといえる。
浸漬前 60日後

120日後

図2.11
硫酸浸漬試験における経時変化(No.22)
図2.12は供試体No.88の硫酸浸漬試験状況を示す。浸漬後60日後の観察において、膨れ、ひび割れ、軟化、溶出は観察されなかった。そ
こで、硫酸浸漬試験を120日まで継続した。硫酸浸漬試験120日での表面観察において、膨れおよびひび割れが観察されたため、硫黄浸透深さ
を評価項目とする遮断性については無いといえる
浸漬前 60日後

120日後 120日後(膨れ) 
図2.12
硫酸浸漬試験における経時変化(No.88)
図2.13は供試体No.1010の硫酸浸漬試験状況を示す。浸漬後60日後の観察において、塗材の色調は変化したが、膨れ、ひび割れ、軟化、溶
出は観察されなかった。そこで、硫酸浸漬試験を120日まで継続した。硫酸浸漬試験120日の表面観察においても、膨れおよびひび割れが観察され
なかったため、遮断性に関して、中性化試験およびEPMA分析による硫黄浸透深さの測定を行うこととした。
浸漬前 60日後

120日後 120日後(膨れ) 
図2.12
硫酸浸漬試験における経時変化(No.88)
図2.13は供試体No.1010の硫酸浸漬試験状況を示す。浸漬後60日後の観察において、塗材の色調は変化したが、膨れ、ひび割れ、軟化、溶
出は観察されなかった。そこで、硫酸浸漬試験を120日まで継続した。硫酸浸漬試験120日の表面観察においても、膨れおよびひび割れが観察され
なかったため、遮断性に関して、中性化試験およびEPMA分析による硫黄浸透深さの測定を行うこととした。
2.2 中性化試験
硫酸浸漬試験において120日経過後に膨れやひび割れが観察されなかった供試体No.1010に対して、中性化試験を実施した。供試体は図
2.14に示すように長手方向の中央と幅方向の中央で、4等分に切断した。
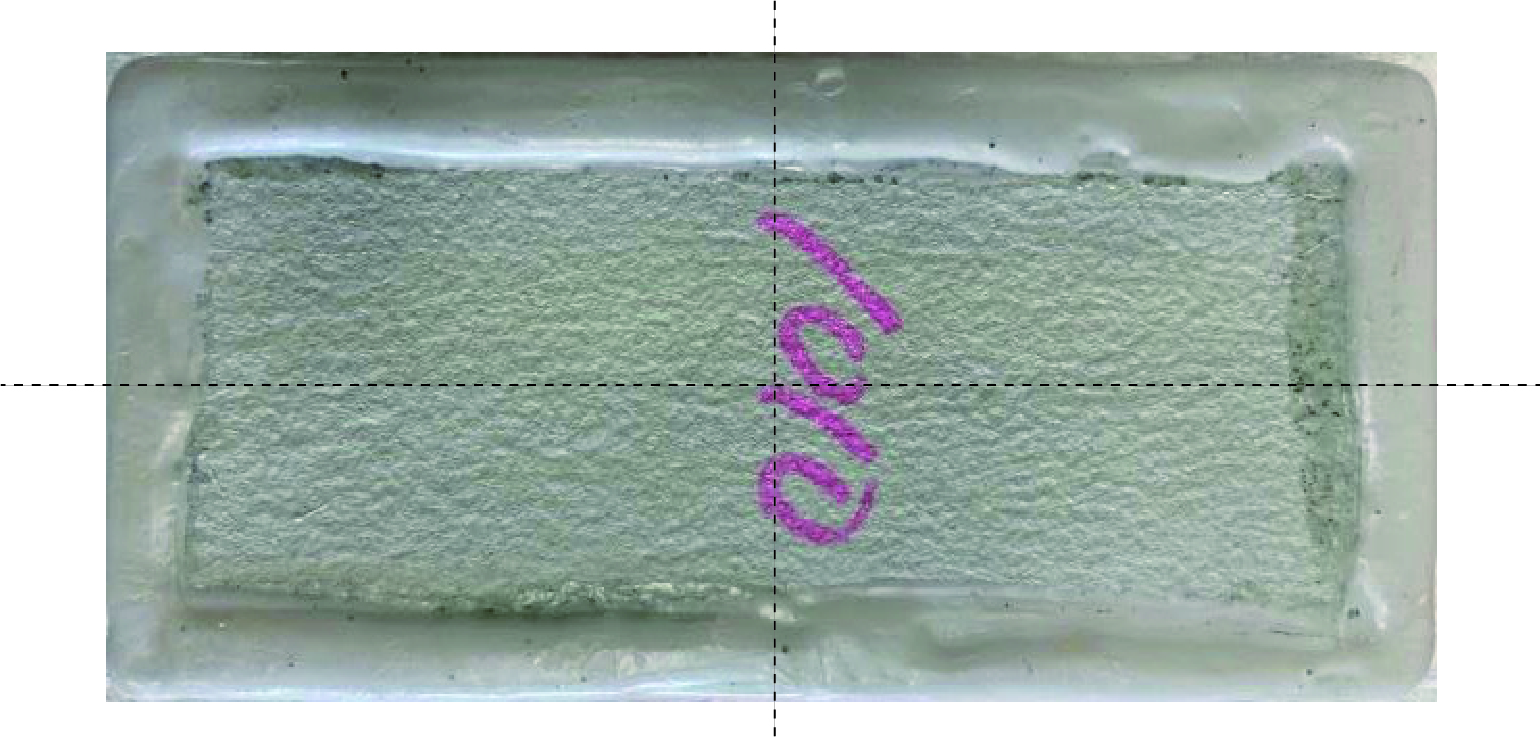
図2.14
供試体 No.1010の切断位置
2.15は供試体の切断面にフェノールフタレインの1%アルコール溶液を散布した後 の状況である。どの面にお いて
も赤紫色を呈しており、中性化していないと言える。このことから、硫酸(HSO)に起因する硫黄(S)は侵入していないと考えられ る。


図2.15
供試体 No.1010の 切断面での中性化の状況
硫酸浸漬試験の120日経過後に膨れやひび割れがなく、中性化試験においても内部で中性化が確認されなかった供試体
No.1010に対して、下水道コンクリート構造物の腐食抑制技術及びマニュアルに規定されている塗布型ライニング
工法の品質規格の要求性能である遮断性を品質規格に従い電子マイクロアナライザー(EPMA:Electron Probe Micro
Analyzer)分析により行った。EPMA分析は株式会社太平洋コンサルタントに依頼した。
EPMA分析には中性化試験で4等分した一つを用いた。試料寸法は縦75mm×横34mm×厚さ19mmである。
EPMA分析はJSCE?G574?2013「EPMA法によるコンクリート中の元素の面分析方法」による。
中性化試験に用いた供試体を図2.16に示すように、ダイヤモンドカッターにより縦方向に切断して、試料片とした。
この試料をメタクリル樹脂で包埋した後、深さ方向のわかる切断面(図2.16の斜線部)を研磨して、分析面とした。
なお、研磨は耐水研磨紙を用いた乾式研磨とし、洗浄液には有機溶剤を用いた。
分析面に導電性を与える目的で炭素を蒸着した後、EPMAによる面分析を行った。

図2.16 試料調製の状況
分析条件および面分析画像の作成条件は以下のとおりである。
使用機器 日本電子社製 電子線マイクロアナライザー JXA?8200
加速電圧 15kV
照射電流 50nA
プローブ径 50μm
ピクセルサイズ 100μm
ピクセル数 縦750×横200(75.0mm×20.0mm)
計測時間 40msec/ピクセル
測定元素 硫黄(S)、カルシウム(Ca)、ケイ素(Si)
標準試料 S:Anhydrite(SO3=58.8%)、
Ca、Si:Wollastonite(CaO=48.3%、SiO2=51.7%)
分光結晶 PET:S、Ca、TAP:Si
スキャン方法 ステージスキャン
濃度換算方法 比例法
測定結果の表示形式
面分析結果をもとに、以下の手順により、試料のA面側から深さ方向における元素濃度とモル比分布曲線を作成した。A面側表面を基点とし、深さ
0.1mm(1ピクセル分)ごとに、面分析結果の画像の横方向に並ぶ400個のピクセル群のうち、骨材のピクセルを除いたセメントペーストに相当
するピクセルの平均値を求めた。また、これらの値を表面からの深さに対してプロットすることにより分布曲線を作成した。
面分析結果を表2.1に、元素濃度分布曲線を図2.17にそれぞれ示す。面分析結果では左側が骨材のピクセルを表示した結果で、右側が骨材のピク
セルは非表示の結果である。両側の最上段の画像は分析面の目視写真であり、それらの以下が面分析画像である。画像の上面がA面であり、下面がB面
である。ただし、A面とB面は硫酸浸漬試験ではどちらも同じ浸漬条件であり、ここでは単に記号として用いている。左側のスケールはA面からの距離
を示し、目盛りは1mm間隔である。また、面分析画像右側にあるカラーバーは表示された色と濃度(%)あるいはモル比の関係を示している。
表2.1
EPMA面
分析結果の一覧
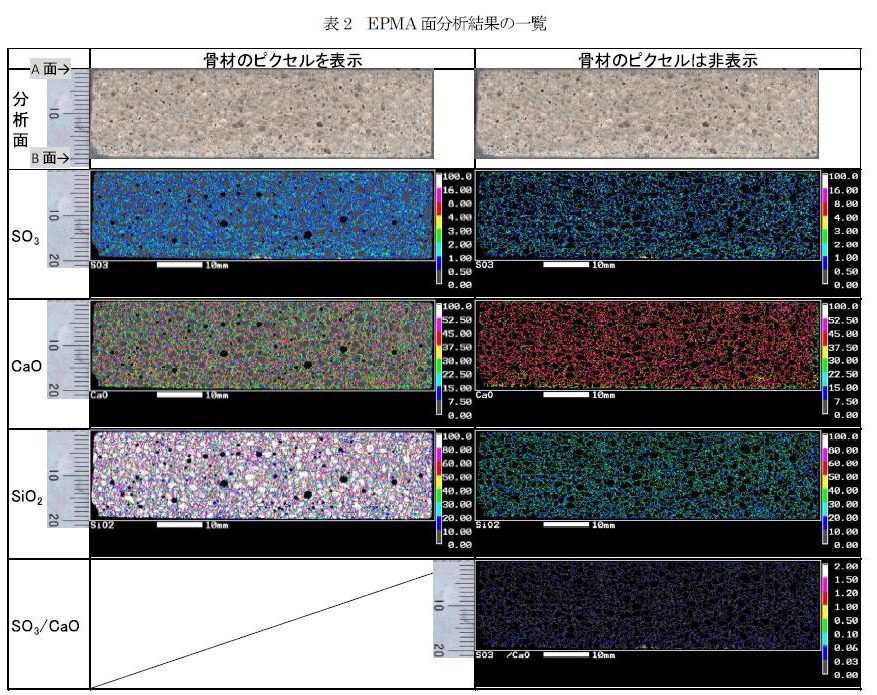
図2.17
元素濃度分布曲線

図2.17より、SO3の濃度はA面側でわずかに高かった。また、B面側では表面の一部に白色で表示されている高い部分が認められた(表2.1の
赤丸)。このほかB面から1.5mm程度においてやや高かった。CaOの濃度はB面側の表面でやや低かった。SiO2の濃度は概ね一定であった。
SO3/CaOの値は主にSO3濃度を反映しており、図2.17よりA面側では表面でわずかに高かった。B面側では、表面のSO3濃度の高い部分
では、黄色から赤色で示されるように(表2.1の白丸)、1前後の高い値を示し、ここでは石膏(CaSO4・2H2O、SO3/CaO=1.0)
が生成していると考えられる。
SO3/CaOの分布曲線から、A面とB面の表面において高くなった値が概ね一定となるまでの距離を硫黄Sの侵入深さとすると、A面からは
1.4mm、B面からは4.2mmとなる。しかしながら、A面近傍において、CaOが少し減少し、SO3はわずかに高い程度でほとんど変化してい
ないことから、SO3/CaOの比が高くなっている。一方、B面近傍ではSO3/CaOの比が増加しているが、SO3も明確に増加している。これ
は石膏の生成によるものであるが、石膏はB面の全域に生成しておらず、一部(赤丸)だけである。従って、この石膏の生成の原因である硫酸は塗材自
身を浸透したのではなく、ピンホール的な欠陥を介して侵入したと思われる。今回は小さい供試体であるため、スプレーではなく塗材を刷毛で塗布して
おり、塗りむらによる欠陥ができたと考えられる。A面近傍のSO3濃度分布から判断すれば
No.1010に使用した塗材にはD種を満足する遮断性を有していると評価できると考えられるが、別の試料でのEPMA分析が必要である。
2.4 抗菌性試験
図1.3に示したように防食塗材を塗布した供試体を活性汚泥に浸漬し,7日間曝気した後の活性汚泥中の一般細菌数を測定した。図
2.18は7日間曝気した後の状況を示す。供試体No.3とNo.5を浸漬した活性汚泥には泡が発生していた

図2.18
抗菌性試験終了時の状況
図2.19は活性汚泥中の一般細菌数を示す。縦軸の一般細菌数は対数目盛で表している。試験は2回実施したが、2回とも
活性汚泥のみの場合に比べ
て、供試体を浸漬したものでの細菌数が多くなっている。特に供試体No.3では2回と最も多い細菌数となっている。これは図2.18に示すよう
に、曝気によって泡がすることからも、No.3には細菌が増殖しやすい要因が含まれていることが考えられる。また、泡が発生しなかった供試体にお
いても、活性汚泥のみの場合の細菌数に比べて大きくなっている。ここで、これまでの試験結果を含めて活性汚泥のみの細菌数を
1×105CFU/mlとすると、2回目の試験において坑廃汚泥を用いた供試体No.6が3.9×104CFU/mlと細菌数が減っている。銅ス
ラグを用いた供試体ではNo.2とNo.5において、低減はしていないが活性汚泥とほぼ同程度の細菌数となっている。そこで、銅スラグの抗菌性を
確認するために銅スラグ微粉末をセメントの一部に置換したモルタル版(CUSモルタル)を比較のために一緒に試験した。CUSモルタル版でも活性
汚泥のみより大きくなっているが、2回目の試験では4.5×140CFU/mlと細菌数が減っている。図2.20は銅スラグ微粉末を置換したモル
タル版に加えて、銅スラグ砂自身と銅スラグ砂を混入した石膏版を用いて試験した活性汚泥の一般細菌数を示す。この実験では活性汚泥。のみの場合の
細菌数が少なくなっており、供試体を浸漬した活性汚泥では一般細菌数が増加している。この原因として、図2.18の試験状況で分かるように、曝気
による気泡の発生が容器によって異なることが考えられたため、曝気を行わないで試験を行った。その結果、曝気を行わない場合には、全てにおいて一
般細菌数に差がみられなかった。

図2.19
活性汚泥中の一般細菌数

図2.20 活
性汚泥中の一般細菌数
 
図
2.21シェー ク法により細菌数
そこで、JISに基づく抗菌性試験を行った。抗菌性試験は大和化学工業株式会社評価技術センターに依頼 した。一般的な抗菌加工製品はは「JIS
Z
2801:2010抗菌加工製品−抗菌性試験方法・抗菌効果」に定められているフィルム密着法に基づいて試験を行うが、時間的問題から既に試料がある銅スラグ微粉末を置換
したモルタル版を用いたシェーク法により試験を行った。図2.21はシェーク法による黄色ぶどう球菌および大腸菌の生菌数を示
す。生菌数の測定方法は寒天平板培養法であり、対照区は試料を投入しない接種用菌液を用いた結果である。図2.21から銅スラグ
微粉末を置換したモルタル版(CUS)は対照区の生菌数より黄色ぶどう球菌および大腸菌どちらも少なくなっている。しかしなが
ら、銅スラグ微粉末を置換していないモルタル版(OPC)と比べるとCUSの生菌数は多くなっている。今回用いた試料は図
2.19の試験に用いたモルタル版と同じものであり、図2.19と図2.21の結果において異なった傾向となっている。このこと
から銅スラグには抗菌性があると考えられるが、確実に発揮されことがないと言える。
3.まとめ
本実験の結果から、供試体No.2、No.8、No.22、No.88、No.1010の供試体に用いた塗材は日本下水道事業団
の「下水道コンクリート構造物の防食抑制技術及び防食技術マニュアル」の塗布型ライニング工法の品質規格におけるD種の耐硫酸性
を有していると言える。さらに、No.1010に用いた塗料においては硫黄の侵入に対する遮断性を有していることを示唆する結果
となった。今回使用したフッ素樹脂自体は硫酸に侵食されることはなかったことから、供試体に塗材を塗布する際にピンホールなどの
欠陥をなくす工夫が必要であり、それにより、No.1010以外の供試体に用いた塗材においてもD種の要求性能を満足する可能性
があると考えられる。
また、抗菌性に関しては活性汚泥を用いた試験においてバラツキがあるが、坑廃汚泥を含むNo.6に用いた塗材において抗菌性を示
唆する結果となった。また、銅スラグにおいては抗菌性に関して不確実性がみられたため、使用する銅スラグ微粉末において銅成分の
含有量を確認した上で、試料を作製して試験を行う必要があると思われる。
|